Design and Prototyping of High Torque Density Dual-Stator PM Machine
Researcher: Shahin Asgari
Supervisor: Mojtaba Mirsalim
(2017-2018)
This project presents a dual-stator permanent magnet synchronous machine (DS-PMSM) with diametrically magnetized cylindrical PMs (DMCPMs). The advantages of the proposed DS-PMSM are its small cogging torque and torque ripple, sinusoidal (low harmonic) air-gap flux density waveforms, a high pole-pair number structure, which can be used to increase the torque density. To confirm the advantage of the proposed DS-PMSMs, first, the cogging torque produced with conventional arc PMs and cylindrical PMs are compared. Next, a DS-PMSM with DMCPMs is designed and its cogging torque calculated. Then, all the relevant machine characteristics, including the cogging torque, air gap flux density, back electromotive force, and torque-angle characteristics are predicted by the two-dimensional and three-dimensional finite element method. Finally, the machine is prototyped and the validity of its advantages investigated with the experimental tests.
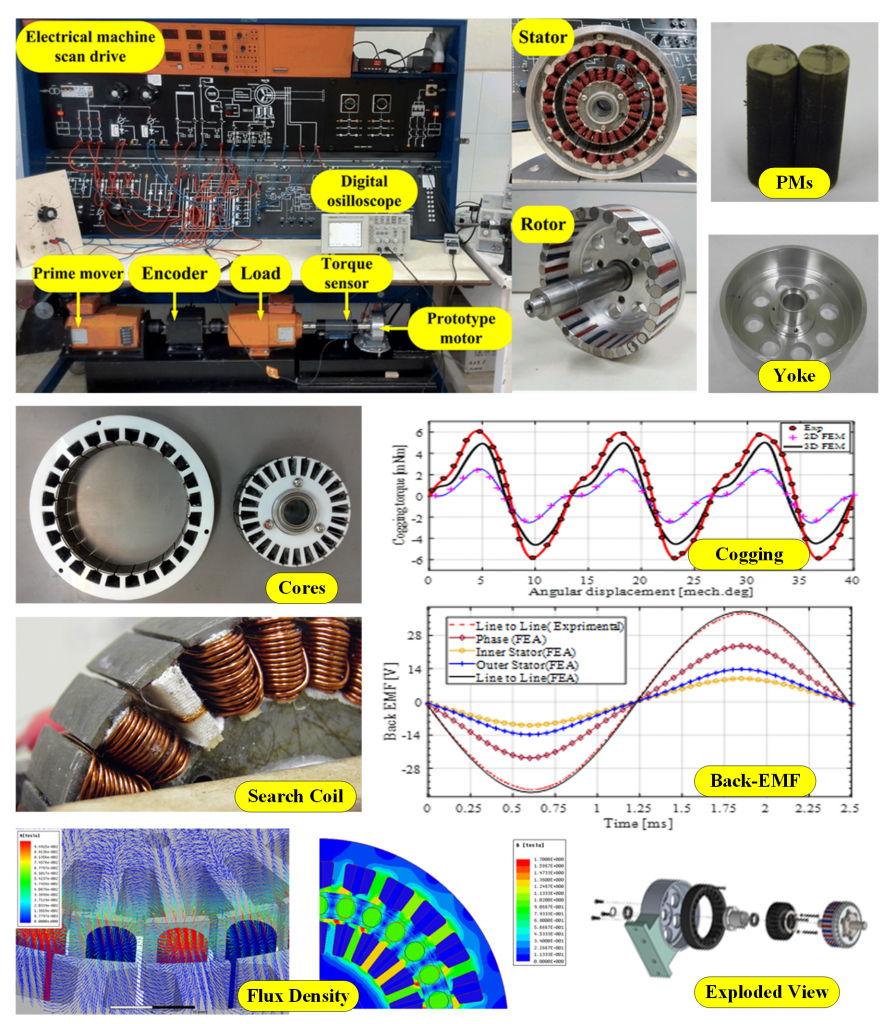
Thermal analysis of a Dual- Stator Machine with Diametrically Magnetized PM and Comparison with Conventional Dual-Stator Machines.
Researcher: Shahin Asgari
Supervisor: Mojtaba Mirsalim
(2016-2017)
Due to the higher rated frequency of the proposed Dual- Stator machine than a conventional machine, the magnets and core losses has slightly increased which it may cause a higher temperature rise in the proposed machine than a conventional structure. The thermal analysis of the design is carried out in 3D FEA to find the temperature distribution and temperature rise in the two machines. For this analysis, the estimated loss components are used as the thermal excitations in the machine model, and the ambient temperature is used as the boundary condition of the problem. In the thermal model of two machines, it is assumed that the copper conductors in the stator windings are solid and their thermal contact resistance with the stator iron core is negligible. The maximum ambient operating temperature is 60 ◦C, and the motors are naturally cooled.
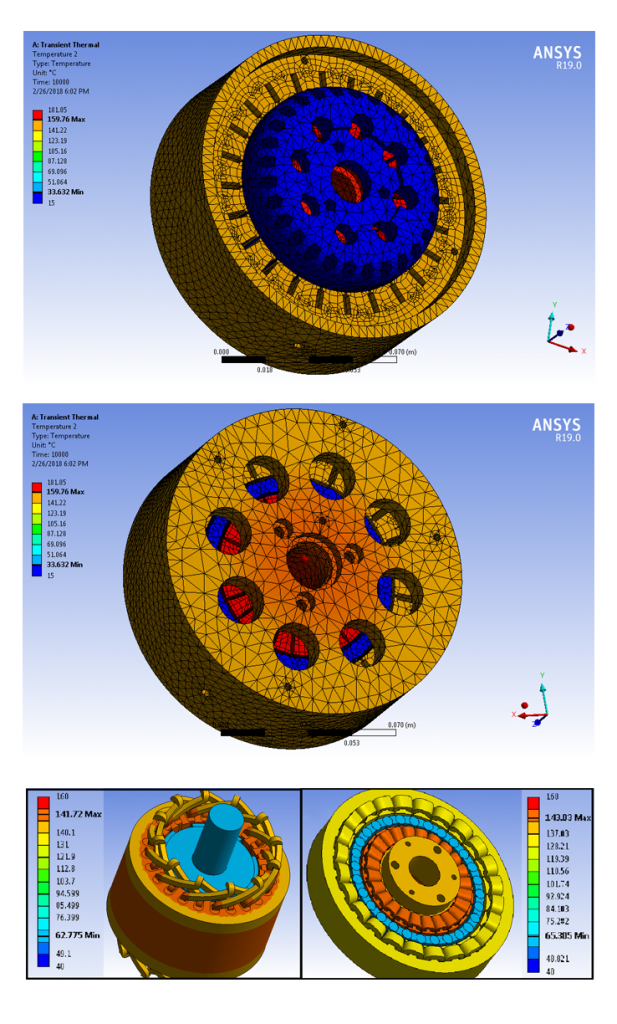
Analytical Air-gap Flux Calculation, Efficiency Optimization of a Dual- Stator Machine with Diametrically Magnetized PM.
Researcher: Shahin Asgari
Supervisor: Mojtaba Mirsalim
(2015-2016)
This project presents a design and optimization procedure for a dual-stator machine with a diametrically magnetized PM to improve the electromagnetic performance. The dual-stator machine is optimized to obtain high efficiency and torque density, and low pulsating torque for direct-drive applications. A quantitative comparison is performed between the optimized dual- stator machine with a diametrically magnetized PM and conventional dual-stator machines to evaluate the contribution of the understudy machine. The machine performance, including air-gap flux density distribution, back electromotive force, electromagnetic torque, cogging torque, and torque ripple are first analyzed by a finite element method. Benefiting from its topology, the analysis results have demonstrated that the optimized dual-stator machine with diametrically magnetized PM has the comprehensively improved performance, including higher torque density, higher efficiency, and lower torque ripple and cogging torque compared to conventional dual-stator machines.
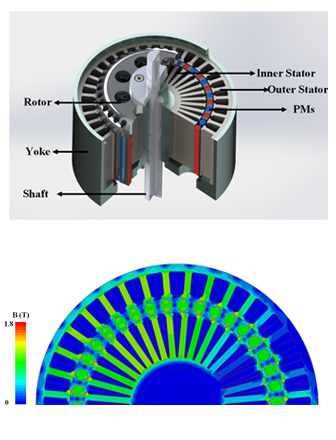
A new E-core hybrid reluctance motor (HRM)
Researcher: Moein Masoumi
Supervisor: Mojtaba Mirsalim
(2014-2017)
In this project, a new E-core hybrid reluctance motor (HRM) is designed with permanent magnets (PMs), placed inside stator common poles. This motor is a 2-phase 12/16 HRM, which is characterized by a stator composed of four E-cores and a rotor with the same configuration of switched reluctance motors. The three poles of each E-core are identified as a common pole in the middle with no windings and two excitation poles in the sides with concentric windings. The windings of the excitation poles are wound such that both phases generate flux in the same direction as the PMs flux, so the demagnetization problem of the PMs is solved. The proposed motor is analyzed, and in order to illustrate the features and improvements, it is compared with two other well-established HRMs of the same size based on the simulation results obtained from the finite element analysis method. Moreover, some parameters like average torque, output power, and efficiency are compared, and it is illustrated that the proposed motor has better specifications compared to the other two. Finally, to verify the accurate design and operation of the proposed motor, its experimental verification is performed.
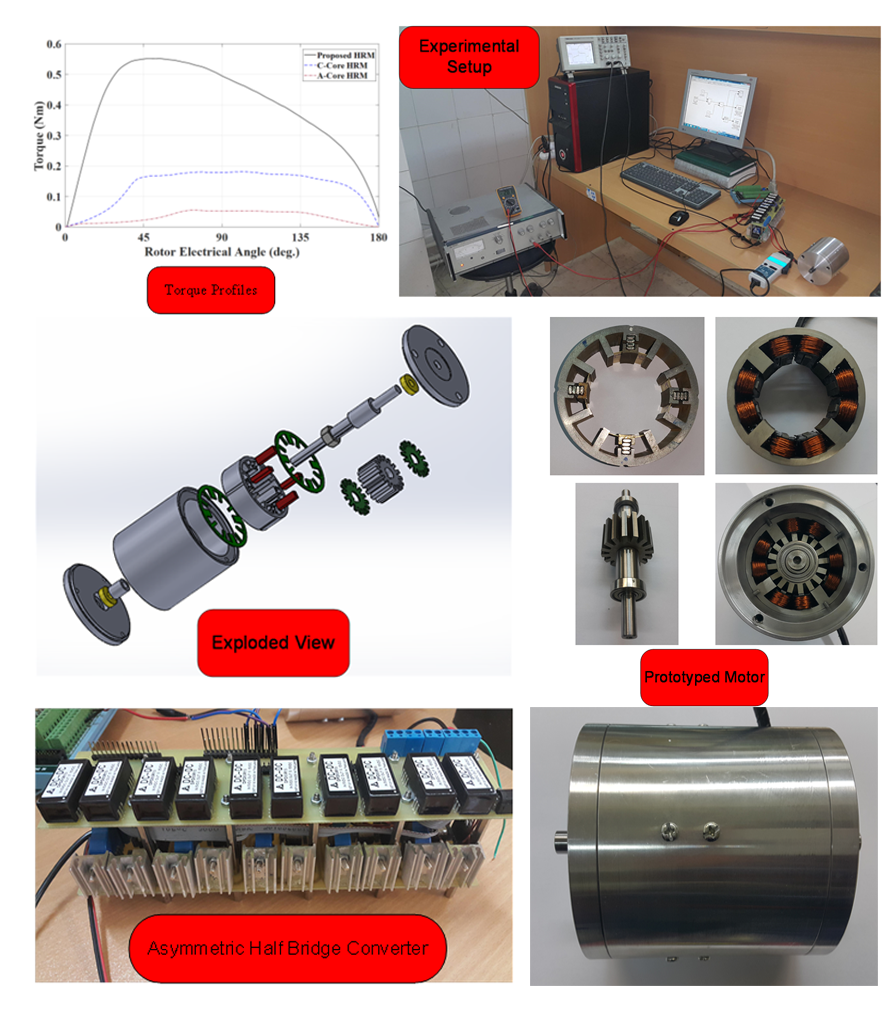
Design and prototyping of a new flywheel energy storage system
Researcher: Ehsan Ghaemi
Supervisor: Mojtaba Mirsalim
(2012-2017)
This study presents a new `cascaded flywheel energy storage system’ topology. The principles of the proposed structure are presented. Electromechanical behaviour of the system is derived base on the extension of the general formulation of the electric machines. Design considerations and criteria are discussed and a general procedure for designing of such energy storage system is developed. Typical machine is designed and an analogy between it and the conventional one is discussed. Comparison shows significant improvements in energy density and utility requirements of the proposed system in comparison to the conventional structure. Dynamic response of the designed machine is studied in various conditions as the stand-alone and also as the grid-connected system. Finally, a typical three-stage system is designed, prototyped and tested which shows a good agreement between an analytical and experimental analysis.
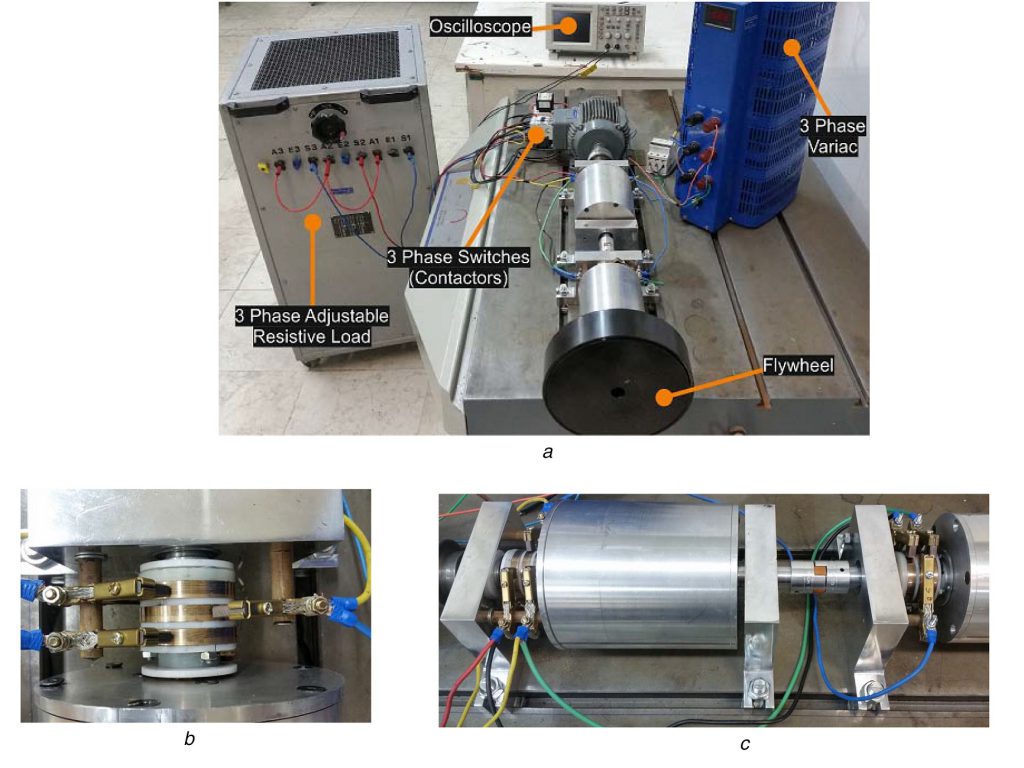
Modeling, design, and prototyping of a hysteresis motor with a novel and optimum structure
Reza Nasiri Zarandi and Mojtaba Mirsalim
(2011-2015)
This project introduces the design and analysis of a new hybrid hysteresis motor with combined axial and radial flux rotors aiming to improve the poor performance characteristics of the conventional hysteresis motors such as the output torque and efficiency. The proposed hybrid design incorporates the advantageous features of both the conventional axial and radial flux hysteresis motors in a unique structure. The design aspects and constraints of the proposed machine are based on a sample single-sided axial flux hysteresis motor. In order to analyze the electromagnetic performance of the proposed structure and investigate the geometry specifications of the designed machine, a 3-D Finite Element Analysis (FEA) is conducted. The hysteresis loop modeling is done based on the elliptical approximation of the hysteresis loop by considering the saturation during the FEA with an iterative method. Also, two analytical models are proposed to analyze the performance of the new hybrid hysteresis motor. At the first method, in order to analyze the electromagnetic performance of the proposed machine and investigate the geometry specifications of the designed machine, the structure is divided into two axial and radial planes and the Laplace’s equation are solved in 2-D Cartesian and cylindrical coordinates for the field in the air-gap, the stator and the rotor disc subject to appropriate boundary conditions. The field equation is modified by the hyperbolic approximation of the hysteresis loop to investigate the effects of the minor loops described by the harmonic components of the field and then, the impact of the Magneto Motive Force (MMF) harmonics on the machine performance is estimated by an iterative approach. Afterward, the closed-form expressions for the developed torque are obtained in both planes and the results are stacked-up linearly by considering the basic of the superposition theorem.
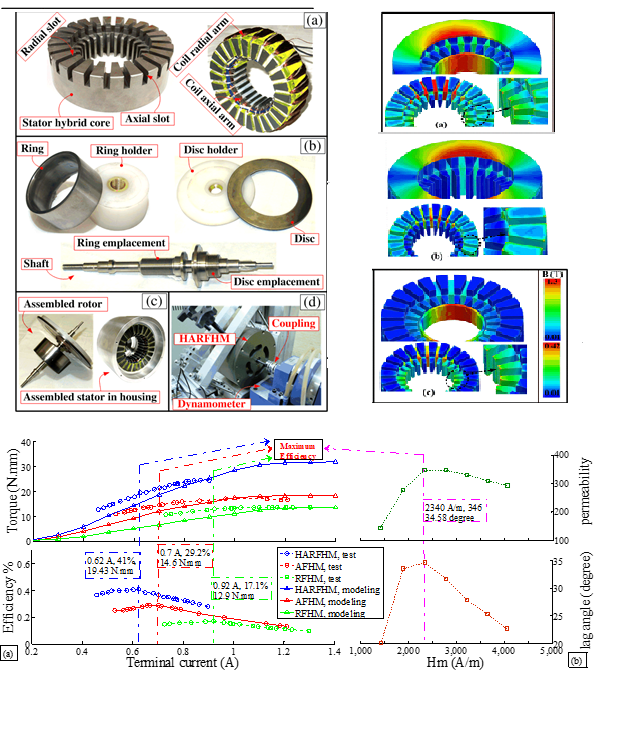
Analysis, design, and prototyping of a hybrid eddy current/regenerative brake
Reza Yazdanpanah and Mojtaba Mirsalim
(2011-2014)
Eddy current brakes having advantages such as contactless operation offer an alternative to conventional friction-based brakes. The flux source in an eddy current brake can be produced by permanent magnets or electrically excited windings. The former eliminates the need for an external supply, whereas the latter provides good control capability for the device. Herein, in order to take the advantages of both mentioned types, a hybrid electromagnetic brake is introduced, and the corresponding design guidelines for the brake part, the complementary part, i.e., the power generating unit, and the interface circuit are presented. Also, design considerations, as well as performance indices associated with the proposed configuration, are discussed. Moreover, the finite-element method is employed in the analyses and versification of the design. Finally, a prototype has been manufactured whose results validate the simulation investigations and the design outcomes.
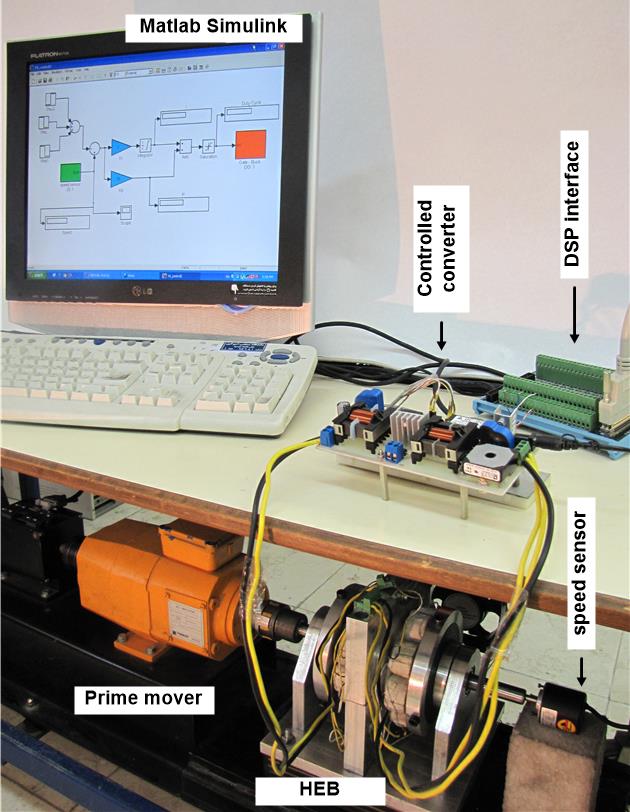
Novel Self-Starting Two-Phase Switched Reluctance Motor: Modeling, Design and Prototyping
Gholamreza Davarpanah and Mojtaba Mirsalim
(2013-2014)
Embedded technology in two-phase reluctance switching machines does not generate electromagnetic torque in certain sequences of the rotor. It means that when the rotor aligns with the middle of stator pole, electromagnetic torque for the related phase induction is zero. Therefore, the inducing winding or the related phase windings do not allow rotor to begin to move from its current place. Hence, these machines are not ignited in stasis, but it is not the case for multiphase reluctance switching machines. A normal question is why three-phase or multiphase reluctance switching machines are not used much more than two-phase reluctance switching machines. The answer is that in fact two-phase reluctance switching machines are equipped with a few control instruments such as power control key and diode in the convertor, while it is not the case in three-phase or multiphase reluctance switching machines. By using less power instruments in the power convertor, the convertor cost as well as the total cost of the motor driver is reduced. Moreover, less power instruments bring higher advantages. For example, it leads to a smaller heat sink device in heat management and fewer gate circuit components in gated power supply. In addition, a two-phase load is controlled rather than three-phase or multiphase loads. These factors contribute in component reduction and simple structure of micro controller of power convertor and thus, the cost of drive motor system is decreased. Therefore, we must find a solution for the problem of self-driven approach in two-phase reluctance switching motors in order to use them.

Novel 8/10 Switched Reluctance Motor with Efficiently Reduced Core: Modeling, Design, and Prototyping
Gholamreza Davarpanah, Sajjad Mohammadi and Mojtaba Mirsalim
(2013-2014)
M.S. thesis of Gholamreza Davarpanah
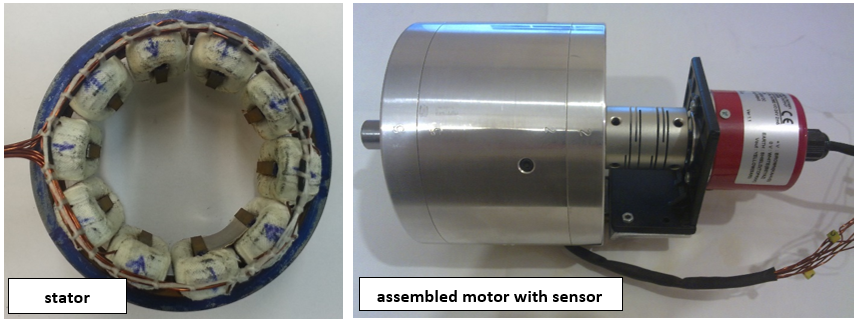
DSP-based Speed Control of a Wound-Excited Eddy-Current Coupler by a Buck Converter
• Sajjad Mohammadi and Mojtaba Mirsalim
(2013-2014)
The control scheme proposed for the device is given in the previous project. The load speed is measured by an encoder that is transferred to MATLAB/Simulink through the digital inputs of the DSP. The controller is implemented in Simulink whose processes output (duty cycle of the power switch) is sent to the buck converter through the digital outputs of the DSP. Output of the buck converter is finally attached to the slip rings to transfer the DC power to the field coils. The following picture illustrates the control setup including the coupler whose secondary part is fixed at prime mover, while its primary is coupled with a speed encoder that measures the speed. The buck converter and the terminal board of the DSP can also be observed. The main DSP board is placed on the mother board of the PM which is connected to the terminal board by a cable. Desktop of the PC including the Simulink blocks and the real-time scopes are also shown in below presents the result for the close loop speed control of the device obtained by a PID controller, in which the measured and the one passed through a low path filter are shown. It is seen that the load speed tracks the speed command with a relatively good response.
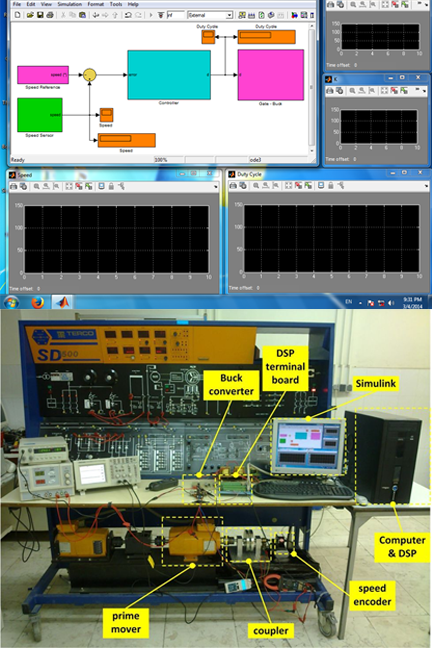
Novel Axial-Flux Wound-Excited Eddy-Current Coupler with Capability of Speed Control: Modeling, Design, and Prototyping
Sajjad Mohammadi and Mojtaba Mirsalim
(2013-2014)
The main contribution of this chapter is to propose a novel wound-field axial-flux eddy-current coupler. In the structures studied in the previous chapters, the magnetic flux was produced by PMs and thus, there is no filed control capability. But, in the proposed wound-field structure, the air-gap flux and thus the torque-speed characteristic of the device could be adjusted. In the other words, a speed control capability is provided. 3-D FEM is also employed in the analysis and evaluation. Finally, a prototype is built to confirm thevalidity of the design.
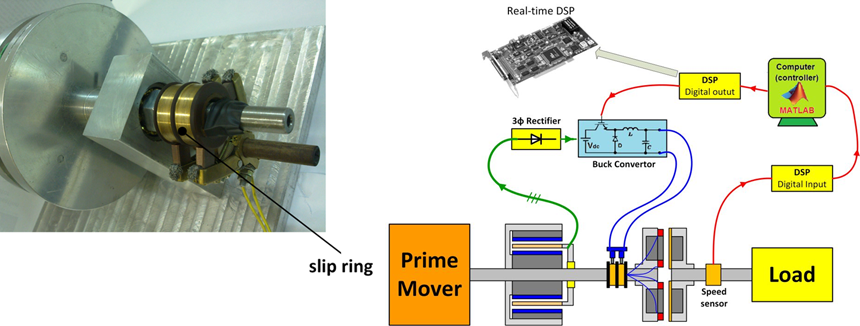